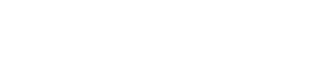
Yan Qin
Leave a messageFunction:
Prevent sand sticking
In lost foam casting, liquid metal easily penetrates into the gap between dry sand under negative pressure. Lost foam coating can form a continuous and dense isolation layer on the surface of the model, preventing liquid metal from directly contacting dry sand, making the surface of the casting smooth, avoiding sand sticking defects, reducing the workload of subsequent cleaning of castings, and improving production efficiency and casting quality.
Improve the surface quality of castings
The coating can fill the tiny bumps and pores on the surface of the model, making the surface of the model smoother, so that during the filling and solidification process of liquid metal, the casting can better replicate the shape and size of the model surface, reduce the surface roughness of the casting, and improve the appearance quality and dimensional accuracy of the casting.
Improve air permeability
The lost foam will quickly vaporize under the heat of liquid metal and produce a large amount of gas. The coating has a certain air permeability, which allows these gases to be discharged smoothly through the coating into the molding sand, and then discharged from the gap between the molding sand to the casting, preventing the formation of defects such as pores and air marks inside the casting due to the inability to discharge gas, and ensuring the intrinsic quality of the casting.
Enhance model strength
Lost foam is usually brittle and has relatively low strength. After the coating is applied to the surface of the model, it can enhance the overall strength and rigidity of the model to a certain extent, making it less likely to be damaged or deformed during transportation, molding and pouring, ensuring that the model can maintain its complete shape, and providing a guarantee for obtaining high-quality castings.
Regulate heat transfer
The coating can regulate the heat transfer process between the model and the liquid metal to a certain extent. It can slow down the thermal shock of the liquid metal on the model, making the model gasification process more stable, and at the same time it can also affect the solidification cooling speed and sequence of the casting, which is conducive to the sequential solidification of the casting, promoting the shrinkage of the liquid metal, reducing defects such as shrinkage cavities and shrinkage, and improving the density and mechanical properties of the casting.
Protect the mold
It can prevent the high-temperature liquid metal from scouring and eroding the mold, and extend the service life of the mold. Especially for some casting materials that use reusable casting materials, such as resin sand, the protective effect of the coating can reduce the loss of casting materials and reduce production costs.
Specifications:
Particle size specifications
Bauxite: Often used as refractory aggregate, the particle size is generally 150 mesh - 325 mesh, such as Yangquan Zhengguang's lost foam bauxite has 200 mesh - 350 mesh products.
Kaolin: The particle size can reach 325 mesh.
Wollastonite: The particle size is usually 200 mesh.
Talc: Generally requires a particle size of 325 mesh.
Sepiolite: Commonly 325 mesh.
CMC: Usually 200 mesh.
Casting powder: There are micron-grade casting powders that reach 4000 mesh.
This website uses cookies to ensure you get the best experience on our website.
Comment
(0)